October 24, 2022
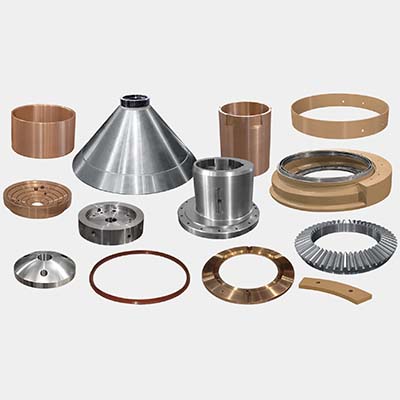
It is essential to select the correct crusher for each task. Understanding
the different stages of crushing and the types of crushers that best fit the
stage makes it easier to select the right equipment. Every crusher type is
unique and designed to get a particular end result.
Like the previous stage every crushing stage is expected produce an exact
output for the next stage. Aggregate producers that are matched to the proper crusher liners stage with the proper
stage will be most efficient and profitable.
The crushing stages
The majority of aggregate producers are acquainted with the selection of
crushing equipment and know it is possible to choose the right equipment solely
on spec sheets and Gradation calculations. However, the theoretical conclusion
should always be evaluated against actual experience with the material at hand
and of the maintenance, operational and economic aspects of various
solutions.
In general, material reduction is handled in stages. There are a few
single-crusher systems that are used, however the majority of systems involve at
least three or two crushing stages.
Primary crushing. Primary crushing is the method used to make it possible to
transport material using a conveyor belt. In the majority of aggregate crushing
plants, the primary crushing process is performed in a jaw crusher, although a
gyratory primary crusher may be used. If material is easily crushed and is not
too abrasive, an impact crusher could be the best option.
A primary crusher's most important attributes are its capacity and ability to
take raw material with no blockages. A large primary crusher is more expensive
to purchase than a smaller model. This is why the initial investment costs for
primary crushers are assessed against the expense of reducing raw materials to
smaller dimensions.
The trucks transport the materials from one location to another. The cost of
fuel, tires, maintenance and return on investment should also be
considered.
A pit-portable primary crusher could be an economically sound solution when
the manufacturer is crushing at the quarry's face. Modern machines often have
the possibility of a mobile primary crusher that can move with the quarry
face.
Intermediate (secondary) crushing. Intermediate crushing is utilized to
create coarser fragments and prepare the material for crushing. The quality of
the final product is essential if the intermediate crusher is to be used for
railway ballast.
In other cases, there are normally no quality standards, however the product
must be suitable for fine crushing. In most cases, the aim is to get the most
efficient reduction for the least cost.
Fine crushing (tertiary). This stage is what determines the quality and
quantity of fine products. The quality requirements may be strict for the final
product, particularly in the aggregate industry.
In most cases the function of fine crushing and cubicization are combined
into a single crushing stage. The choice of the appropriate crusher for tertiary
crushing demands the combination of practical and the theoretical knowledge.
This is where producers should make sure they call an experienced specialist in
applications to ensure that the machine is designed and constructed
correctly.
Types of crushers
Jaw crushers
Jaw crushers are a compression type of crusher. The material is reduced by
compressing the material that feeds it between a moving piece steel and a
stationary piece. The setting or distance between two steel pieces, controls the
discharge size. The setting is tighter which results in an output that is
smaller and a lower capacity for throughput.
As a compression crusher jaw crushers generally produce the coarsest material
because they break the rock using the natural lines of weak points. Jaw crushers
can be utilized as primary crushers to make the rock ready for processing
later.
Cone and Gyratory crushers
They also crush steel between two steel pieces. The position between the two
pieces controls the output.
The chamber is circular in shape however, the steel piece is not intended to
turn. Instead, a wedge is driven around to cause compression on the one side and
discharge opening on the opposite side. Cone crushers are employed in secondary
and tertiary roles in lieu of impact crushers in cases where shape is an
important requirement, but the proportion of fines produced must be
reduced.
Impact crushers
An impact crusher uses the force and velocity of the machine in order to
reduce feed material. The material feed is reduced when it enters the crusher
liners through the rotating blow bars or hammers inside the rotor. The second
breakage occurs when the material is brought up into the stationary aprons , or
breaking plates.
Impact crushers are usually used where the shape of the product is important
and the feed material isn't very hard and abrasive. The crushing action of an
impact crusher breaks rocks along natural cleavage planes, giving rise to better
product quality in regards to shape.
Final thoughts
When selecting the crusher to best suit your operation it is crucial to
comprehend the needs of each stage.
In the first stage, you must get material that is large enough to support
your conveyors as well as other equipment for processing.
Certain operations require additional crushing in the secondary or tertiary
stages. These stages allow for better control over the size and form of the
final product.
Understanding how to best match the crusher with the appropriate crushing stage will guarantee the highest level of efficiency in your crushing process and will ultimately improve your overall profit.
Posted by: NatheniBarker at
05:37 AM
| No Comments
| Add Comment
Post contains 910 words, total size 7 kb.
35 queries taking 0.0604 seconds, 75 records returned.
Powered by Minx 1.1.6c-pink.